Just how to Recognize What is Porosity in Welding and Improve Your Strategy
Just how to Recognize What is Porosity in Welding and Improve Your Strategy
Blog Article
Porosity in Welding: Identifying Common Issues and Implementing Best Practices for Prevention
Porosity in welding is a prevalent problem that frequently goes unnoticed till it triggers significant troubles with the stability of welds. In this conversation, we will discover the key factors adding to porosity formation, examine its destructive impacts on weld performance, and review the finest techniques that can be adopted to decrease porosity occurrence in welding processes.
Usual Reasons of Porosity
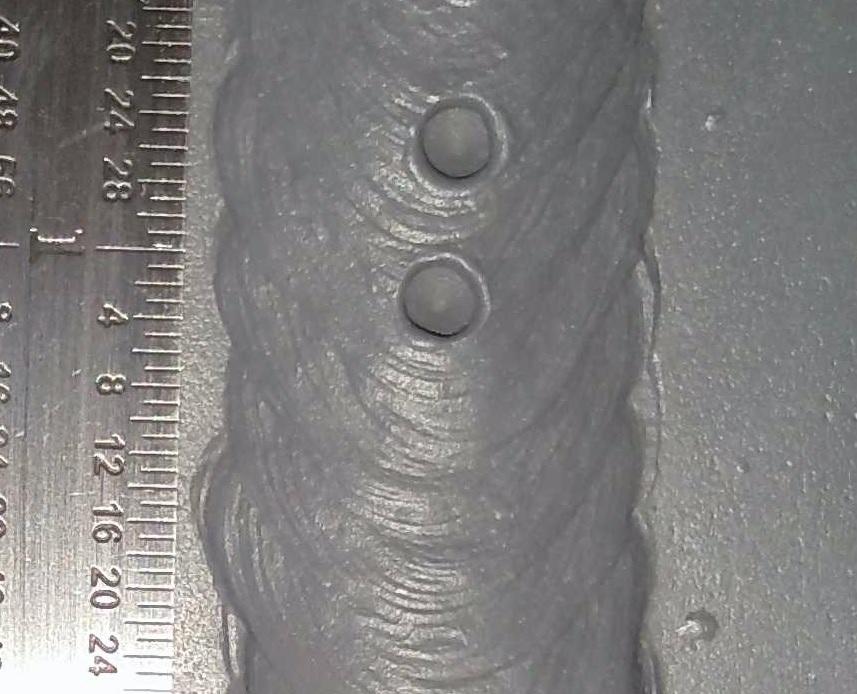
Another regular perpetrator behind porosity is the presence of pollutants externally of the base steel, such as oil, grease, or rust. When these contaminants are not effectively removed before welding, they can evaporate and come to be trapped in the weld, causing defects. Furthermore, using unclean or damp filler products can introduce contaminations right into the weld, adding to porosity problems. To mitigate these common root causes of porosity, detailed cleansing of base metals, proper securing gas option, and adherence to ideal welding parameters are important methods in accomplishing top notch, porosity-free welds.
Impact of Porosity on Weld Quality

The presence of porosity in welding can significantly compromise the architectural stability and mechanical residential properties of bonded joints. Porosity produces voids within the weld steel, deteriorating its general strength and load-bearing ability. These gaps serve as stress and anxiety concentration factors, making the weld more prone to cracking and failure under used lots. Furthermore, porosity can lower the weld's resistance to corrosion and other ecological factors, additionally lessening its longevity and efficiency.
Among the key repercussions of porosity is a decrease in the weld's ductility and sturdiness. Welds with high porosity levels often tend to exhibit reduced impact stamina and reduced capability to flaw plastically before fracturing. This can be specifically concerning in applications where the bonded parts go through vibrant or cyclic loading conditions. Moreover, porosity can impede the weld's capability to properly transmit pressures, leading to premature weld failing and possible security threats in crucial frameworks.
Ideal Practices for Porosity Prevention
To boost the architectural integrity and quality of bonded joints, what More hints details measures can be implemented to minimize the occurrence of porosity during the welding process? Porosity prevention in welding is essential to guarantee the integrity and toughness of the final weld. One reliable method appertains cleansing of the base check it out steel, getting rid of any kind of impurities such as corrosion, oil, paint, or wetness that might result in gas entrapment. Making sure that the welding equipment remains in great problem, with clean consumables and proper gas circulation rates, can also significantly reduce porosity. In addition, keeping a steady arc and managing the welding parameters, such as voltage, current, and travel rate, helps develop a consistent weld swimming pool that minimizes the danger of gas entrapment. Utilizing the appropriate welding strategy for the details material being welded, such as readjusting the welding angle and gun setting, can further avoid porosity. Normal inspection of welds and prompt remediation of any concerns identified throughout the welding procedure are important practices to avoid porosity and generate top quality welds.
Value of Appropriate Welding Methods
Implementing appropriate welding strategies is paramount in ensuring the structural integrity and top quality of bonded joints, building on the foundation of efficient porosity avoidance actions. Welding techniques directly affect the overall strength and resilience of the bonded framework. One crucial element of proper welding techniques is preserving the right warmth input. Too much heat can result in boosted porosity as a result of the entrapment of gases in the weld swimming pool. Alternatively, insufficient warmth may result in insufficient combination, creating potential powerlessness in the joint. Furthermore, utilizing the appropriate welding criteria, such as voltage, present, and travel rate, is crucial for achieving audio welds with very little porosity.
Moreover, the option of welding procedure, whether it be MIG, TIG, or stick welding, should line up with the specific requirements of the project to make certain ideal results. Proper cleansing and preparation of the base metal, along with choosing the best filler product, are also necessary components of skilled welding strategies. By adhering to these ideal methods, welders can minimize the threat of porosity formation and produce premium, structurally audio welds.
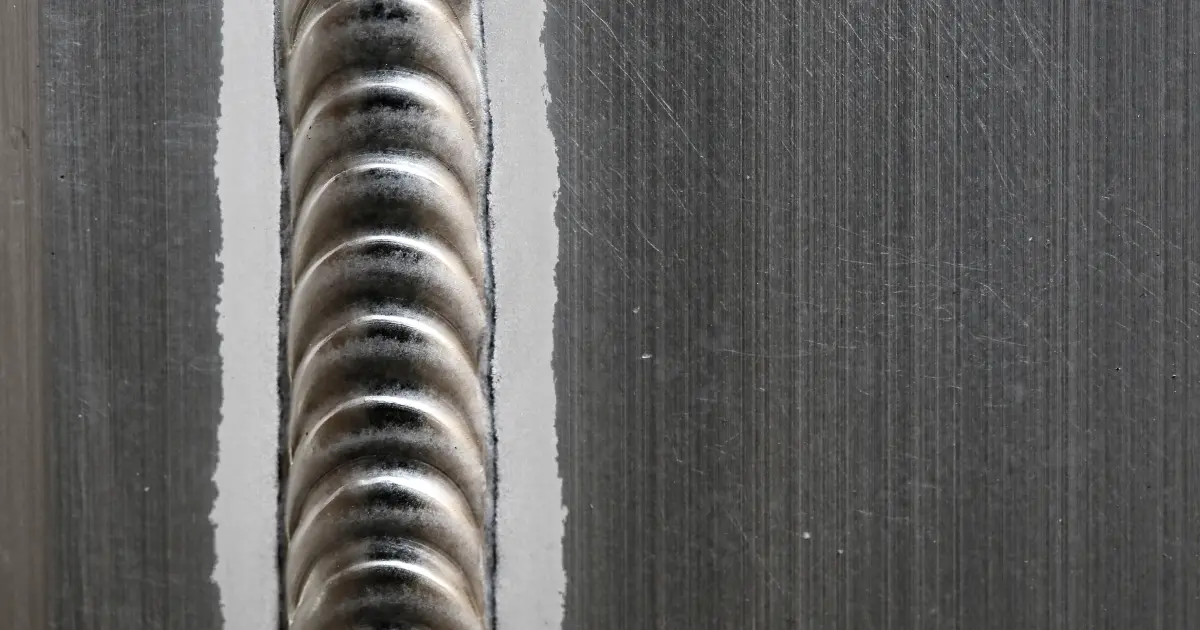
Checking and Top Quality Control Measures
Quality control procedures play an important role in validating the stability and reliability of bonded joints. Evaluating procedures are important to discover and prevent porosity in welding, making certain the strength and sturdiness of the last item. Non-destructive screening approaches such as ultrasonic screening, radiographic testing, and aesthetic inspection are generally employed to recognize potential issues like porosity. These techniques enable the evaluation of weld top quality without jeopardizing the stability of the joint. What is Porosity.
Conducting pre-weld and post-weld inspections is additionally vital in maintaining quality assurance requirements. Pre-weld inspections involve verifying the materials, tools settings, and cleanliness of the job area to avoid contamination. Post-weld assessments, on the other hand, assess the last weld for any flaws, including porosity, and validate that it fulfills defined criteria. find Applying a thorough quality assurance strategy that consists of extensive screening procedures and evaluations is critical to lowering porosity issues and making certain the general top quality of welded joints.
Conclusion
To conclude, porosity in welding can be a common issue that affects the top quality of welds. By recognizing the common reasons of porosity and executing ideal methods for avoidance, such as correct welding strategies and screening measures, welders can guarantee premium quality and trustworthy welds. It is vital to focus on avoidance approaches to minimize the occurrence of porosity and maintain the honesty of welded frameworks.
Report this page